In conclusion, at present, the situation of motor energy saving in China is grim, and increasing the motor energy efficiency rating is the only way to save energy for the motor.

Copper rotor technology is recognized as the industry's most efficient motor technology solutions in the most economical and simple solution. Copper rotor motor has four major advantages:
Improve efficiency Copper rotor instead of aluminum rotor can significantly improve the efficiency of small and medium-sized motors, energy-saving benefits. Taking Y132M-4 7.5KW motor as an example, the efficiency of the motor is increased from 87% to 90.4% after replacing the cast bronze rotor. In accordance with the calculation of ten years using the motor, can save electricity 16,080 yuan, 16 times the replacement cost, the benefits are obvious. Currently, Nanyang Explosion Protection Group has developed a copper rotor induction motor IE5 efficiency level, the actual measured efficiency of 15HP-4P motor up to 93.6%.
2. Reduce temperature rise. Taking a 25HP 18.7KW motor as an example, the use of a copper rotor motor reduces the temperature rise by 41% compared to the aluminum rotor motor, with only 47.2 ° C. The motor operating temperature is reduced by 10 degrees Celsius, the service life can be doubled. Therefore, the copper rotor motor can effectively extend the life of the motor. At the same time also increase the electrical safety, especially for explosive special environment.
3. Reduce the volume, reduce weight, reduce costs. Under the same efficiency, the volume of cast bronze rotor motor is reduced by about 15% compared with that of aluminum rotor motor. It is suitable for the application of base motor, such as reducer motor, compressor motor and pump motor. By optimizing the design, cast bronze rotor motor weight can be reduced by about 20%. Such as: 15 HP TEFC motor converted to cast bronze rotor to reduce the total weight of 8KG. Cost, the same efficiency cast bronze rotor motor can be reduced by about 10%. When the price of copper is reduced or the price difference between copper and aluminum is reduced, the cost reduction will be more obvious.
4. Corrosion resistance. Copper has excellent corrosion resistance makes the copper rotor is very suitable for applications such as brine pumps, hot water circulation pump.
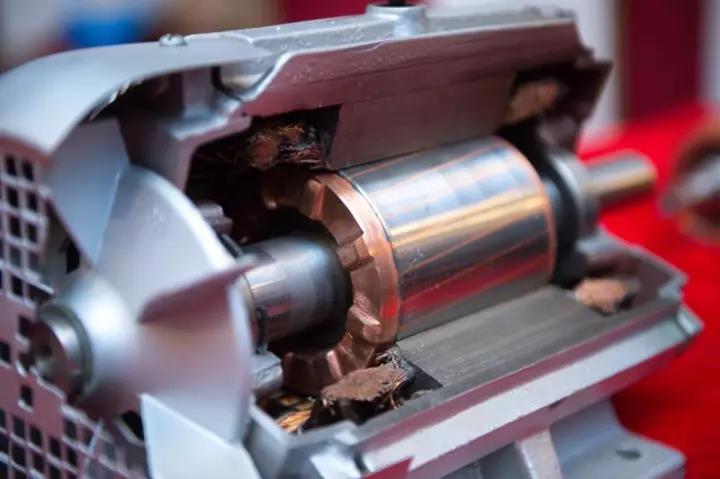
At present, "the energy efficiency of small and medium-sized three-phase asynchronous motor efficiency and energy efficiency rating" made clear in the future all 0.75KW-375KW motor must meet the three energy efficiency indicators (IE2-efficient); of which, 7.5KW-375KW motor in 2016 must Achieve Level 2 Energy Efficiency Indicator (IE3 - Very Efficient); and 0.75KW-7.5KW Motor Must Achieve Level 2 Energy Efficiency Indicator in 2017.
With the continuous improvement of motor energy efficiency rating, the demand for high-efficiency motors will increase substantially in the future. "Small and medium motor industry," Thirteen Five "Development Plan" also proposed: product miniaturization and lightweight, the use of advanced technology and new high-quality materials, focusing on the development of high-power density, high reliability products. This also shows that copper rotor will inevitably become the trend of efficient induction motor.
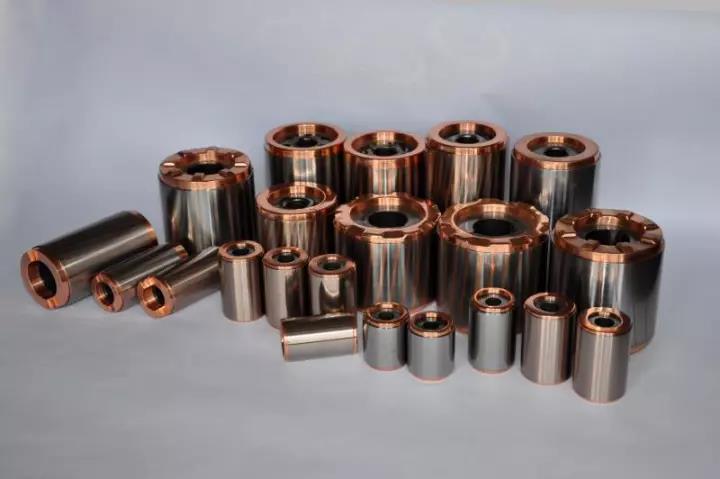
Motor remanufacturing process requires strict adherence to four principles:
Quality: (Strict compliance with remanufacturing process specifications, good quality control remanufacturing process)
Efficient: (improve efficiency, save costs and create more product value)
Energy-saving: (to achieve maximum remanufacturing process efficiency, to achieve the purpose of energy-saving materials)
Environmental Protection: (to improve the utilization of old machine parts, reduce the number of new replacement parts, while improving the technical level of remanufacturing process, reduce the emission of harmful substances)
Contact:Shanghai Wind Automation Equipment Co.,Ltd
Email:emily@motor-machinery.com
Skype: motor.machinery
Mobile: +86-18067425780
Website: www.motor-machinery.com;www.coilswinding.com